By: Jeff Jewitt
Finishing is one of the biggest bugaboos for many woodworkers. Though they remain undaunted by complex joinery or intricate and precise machining, scores of woodworkers still cringe at the thought of applying a finish to their work. "What's the best finish for my project?" is a question I often hear. Being able to answer that question confidently and comfortably is an important hurdle to overcome.
Finishing products can be grouped into manageable categories, based on general working qualities and the degrees of protection they offer: waxes, oils, varnishes, shellacs, lacquers and water-based finishes. Different finishes offer varying degrees of protection, durability, ease of application, repairability and aesthetics. Unfortunately, no single finish excels in all of these categories -- a finish that excels in one may fail in another -- so in choosing a finish you must accept trade-offs.
As a professional refinisher, I routinely ask my customers a series of questions to determine the best finish for their furniture. I've modified my standard questions for this article and added a few as a Checklist for woodworkers trying to decide which finish to use on their own projects. Answers to these questions will point you toward the right finish to use on a given project, based on how well you need to protect the surface, how well the finish will hold up, how easy it is to apply and how you want it to look. To get a better understanding of the choices, let's first take a look at the different categories of wood finishes.
All wood finishes can be classified as one of two distinctly different types, based on how they dry, or cure. Evaporative finishes--such as lacquer, shellac and many water-based finishes--dry to a hard film as the solvents evaporate. (Water is not a solvent -- it's a carrier for the finish emulsion.) These types of finishes will always redissolve in the solvent used to thin them, long after they've dried, so they tend to be less durable than reactive finishes. Most reactive finishes -- such as linseed or tung oil, catalyzed lacquers and varnishes -- also contain solvents that evaporate, but they cure by reacting with either air outside the can or a chemical placed in the can before application. These finishes undergo a chemical change as they cure, and after that they will not redissolve in the solvent originally used to thin them. Except for the pure oils, reactive finishes tend to hold up better to heat and chemicals. See Common finish products compared for a summary of how the finishes stack up against each other.
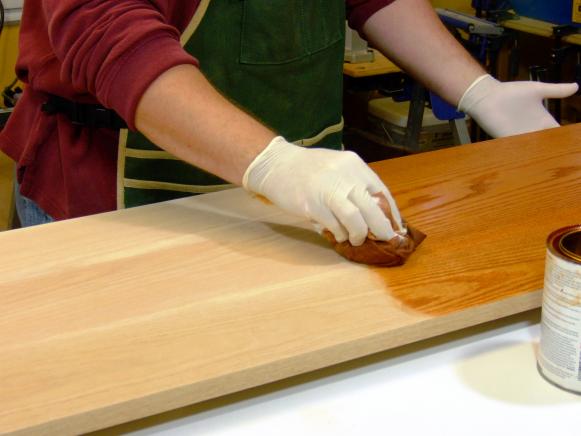
Waxes -- I don't consider wax an appropriate finish in and of itself. I use paste wax (carnauba mostly, sometimes beeswax) to polish furniture but only over other finishes, such as lacquer or shellac.
The true oils -- Linseed oil and tung oil, the drying oils most often used in finishing, are readily available and relatively inexpensive. These finishes are called true oils to distinguish them from other products hyped as oil finishes and to separate them from naturally nondrying or semidrying oils used in finishes, such as soybean oil. These true oils change from a liquid to a solid through polymerization, a process that strengthens the cured finish.
Linseed oil is available in several forms. Unrefined, it's called raw linseed oil, which is rarely used on wood because it dries so slowly. Finishers long ago discovered that by boiling the oil, the resulting product was thicker and dried more quickly. Even though linseed oil that has actually been boiled is still available -- it's called heat-treated or polymerized oil -- most of the boiled linseed oil sold these days is raw oil that has been mixed with chemical additives to speed up the drying time. For wood finishing, you should use only boiled linseed oil.
Tung oil is derived from the nuts of trees that are native to Asia but have been cultivated in other parts of the world. Tung oil is available in a pure, unrefined form and in a heat-treated or polymerized form. The heat-treating process makes the oil a bit more durable and speeds up the drying time. It also minimizes a tendency of tung oil to "frost" (dry to a whitish, matte appearance). Tung oil is paler in color and has better moisture resistance than linseed oil.
Both linseed and tung oils are penetrating finishes, which means they penetrate the fibers of the wood and harden. These are the easiest finishes to apply: Wipe them on, allow them to penetrate the surface of the wood and wipe off the excess with a rag. These oils are usually not built up with enough coats to form a surface film, like that of varnish or lacquer, because the film is too soft.
Varnishes -- Varnish is made of tough and durable synthetic resins that have been modified with drying oils. Labels on cans of varnish will list resins such as alkyd, phenolic and urethane, and the oils used are tung and linseed, as well as other semidrying oils such as soybean and safflower. Varnish cures by the same process as true oils -- polymerization -- but the resins make this finish more durable than oil. In fact, oil-based varnish is the most durable finish that can be easily applied by the average woodworker. Varnish surpasses most other finishes in its resistance to water, heat, solvents and other chemicals.
Varnishes that contain a high percentage of oil are called long-oil varnishes. These include marine, spar or exterior varnishes and some interior varnishes for sale on the retail market. Long-oil varnishes are more elastic and softer than medium- and short-oil varnishes that contain a lower percentage of oil. Medium-oil varnishes comprise most interior varnishes on the market. Short-oil varnishes (also known as heat-set varnishes and baking enamels) require extremely high temperatures to dry, so they're used only in industrial applications.
The type of resin used in the varnish determines the characteristics of the finish. Alkyd varnish is the standard all-purpose interior variety with decent protective qualities. Phenolic varnish, usually made with tung oil, is predominantly for exterior use. Urethane varnish, also called polyurethane, offers a better resistance to heat, solvents and abrasions than any other varnish.
Varnish is typically applied with a brush, although a highly thinned and gelled version, called wiping varnish, can be applied with a rag.
Oil and varnish blends -- These mixtures, mostly oil with some varnish added, offer some of the best attributes of both ingredients: the easy application of true oils and the protective qualities of varnish. (Watco-brand Danish oil, teak oil and a number of other finishes fall into this category.) It's difficult to ascribe accurate protective qualities to these products because manufacturers don't usually disclose the ratio of oil to varnish. Oil and varnish blends will dry a bit harder than true oils, and the finishes will build quicker with fewer applications.
Shellacs -- While most people think of shellac as a liquid finish found at a paint store, in its pure form it's a natural resin secreted from a bug that feeds on trees, mostly in India and Thailand. The secretions, in the form of cocoons, are gathered and eventually refined into dry flakes, which are then dissolved in denatured (ethyl) alcohol to make the shellac solution that winds up in cans at the store.
Shellac is available in several varieties. You can buy it premixed, or you can buy it in flake form and mix it yourself with denatured alcohol. The premixed variety is available in orange (amber) and clear, which is shellac that's been bleached. With the flakes, shellac is available in a wider variety of colors and wax contents than with the premixed version (which contains wax). The wax in shellac decreases the finish's resistance to water and prevents some finishes from bonding to it.
Lacquers -- Most professionals still regard lacquer as the best all-around finish for wood because it dries fast, imparts an incredible depth and richness to the wood, exhibits moderate to excellent durability (depending on the type used) and rubs out well. There are several different types of lacquer, and they exhibit different performance characteristics.
Water-based finishes -- Water-based finish contains some of the same ingredients as varnish and lacquer -- notably urethane, alkyd and acrylic -- but many flammable and polluting ingredients have been replaced with water. The chemistry in this product is complex. Because the resins don't have a natural affinity for water, they must be chemically modified or forced to combine with water.
Water-based finish is usually made with either an acrylic resin (sold as water-based lacquer) or an acrylic urethane mixture (sold as water-based polyurethane). As with varnish, the addition of the urethane makes the resin tougher and more scratch resistant, but water-based urethane does not have the same solvent and heat resistance as its oil-based counterpart.
Article Source:
Furnexindo.com